The Comet wing section was based on a NACA 63A011. The Comet wing had to be extremely thin to achieve the low drag necessary with the first-generation centrifugal jet engines, and yet produce enough lift at the right altitude to make it economically viable. To put the available thrust in perspective, a small, modern, executive jet has more total thrust from two engines than the Comet 1 had from all four.
The Comet 1 wing achieved the required performance at altitude, and low wing-loading ensured good performance when it had to mix with slower-moving traffic, but it stalled at a very low angles of attack. This did not help on take-off, and contributed to two airframes being written off: G-ALYZ in Rome, and CF-CUN in Karachi, the latter with the loss of all on board.
In the 1930s, Handley Page did a lot of research on improving the performance at the leading edges of wings. They found that leading edge slats delayed the stall to higher angles of attack, and made the stall softer, and more easily predictable. They became a useful add-on for very slow, short-take-off aircraft such as the Fieseler Storch. The idea of retractable slats for faster aircraft was experimented with, but without modern metals and servo-mechanisms, they were heavy and unreliable.
After the war, the emphasis was on speed and thin swept-back wings. Experimental aircraft, like the DH-108 Swallow, had very poor low-speed performance. DH-108 prototypes were used not only for high-speed research, but also to improve the performance of high-speed aircraft at low speed as well, for take off and landing.
Results from this research were too late for the Comet 1, but the Comet 2 benefited from modifications to the leading edge of the wing, known as “leading edge droop”.
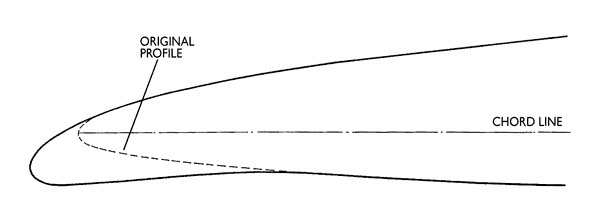
This provided an efficient, light-weight solution, with some of the benefits of leading edge slats, but with only a small increase in drag. Leading edge droop does not increase the basic lift of the aerofoil, but it provides a small gain in the rate of change of lift with angle of incidence, and a considerable one in delaying separation, and therefore the onset of a stall. In X-Plane Airfoil Maker, its effects can be approximated by increasing the lift
slope and
alpha max. Because the maximum angle of incidence is higher, the maximum lift becomes higher, following the trend of the lift slope. As a rough guide, the proportional increase in lift at any point on the slope,
delta 2, tends to be about half the proportional increase in maximum angle,
delta 1.
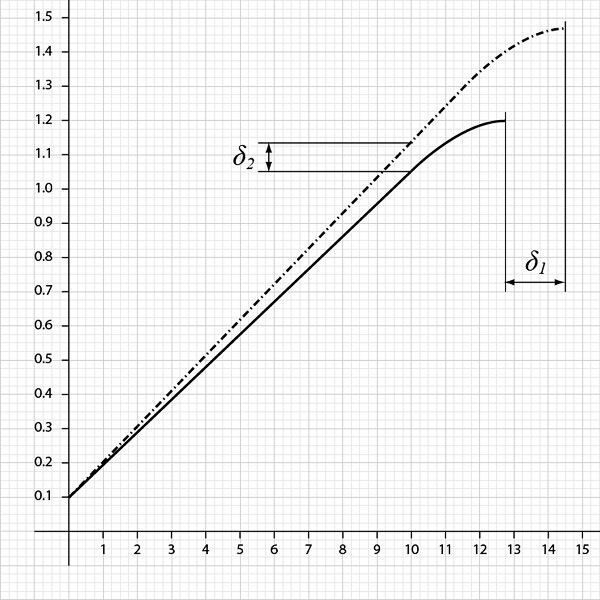
In 1967, the Ministry of Aviation published a report of tests on a Handley Page Victor wing. The report described how leading edge droop could delay separation from 11º (unmodified) to a maximum of 18.5º . The report suggested that an installed modification would be more modest, but it is interesting to know the upper limit.
--
GMM-P (09/01/2010)
Tags: Performance, Aerofoils